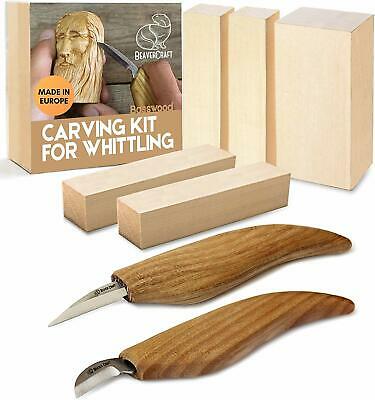
You can carve your own vision if you have always wanted to. Follow along with a photo trail to learn how to do it. This can help you to imitate a famous carving without having to spend hours researching the styles. It's important that your eyes are as accurate as possible. You'll have lots of fun and will likely have great eye-hand coordination. Don't worry if you haven't been a skilled carver before. There are many easy methods to achieve realistic-looking vision.
Lesson 4 Carving hair
This tutorial will guide you through the steps of carving a flowing hairstyle on your animal carving. It will help you create a realistic appearance and create the illusion of lifelike emotion. The video will show you how to create different textures and styles of hair. You will also be able to learn how to make different levels of haircuts using curved tools. Once you are familiar with the basics, the next step is to learn how to work on the more complex areas of the face such as the eyeballs.
You should first outline your eye cavities using a pencil. Next, draw an extended straight line from your eyebrows and eyelids. To make your forehead rounder and higher, you can use a pencil. Afterward, use a whittling sloyd knife to round the corners of the cheeks and bottom lip, as well as the beard area.
Lesson 5 Carving the feet for the crow
If you are prone to crow's feet, then you should know what causes them. These wrinkles can be caused by repeated facial expressions such squinting. Crow's feet are caused by repetitive facial expressions like squinting. You can also use facial moisturizers to prevent the formation of crow's feet.
Fine lines and wrinkles on the face make people appear older than their years. You can easily get rid of these lines and reveal a younger complexion. Here are some helpful tips.
Lesson 6: Carving iris
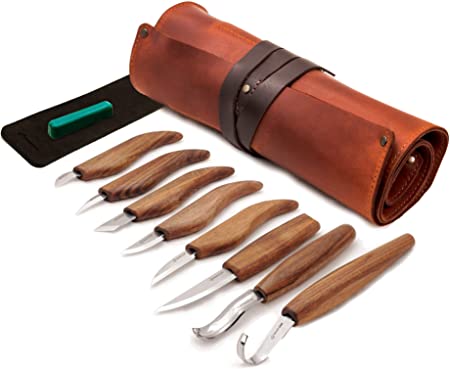
Children can see the iris, ocellus and other parts of their bodies in a mirror. This will help them to understand how they feel and look. They can also use observational drawing and a mirror to draw their own eyes. They can find white or other colours in the iris, and black in the center. After they've finished drawing, they can add color using different media to create depth illusions. Children can then compare the colours in their eyes by looking at one another's drawings.
FAQ
What is the difference in a hobbyist and professional woodworker?
Hobbyists love making things from wood while professionals are more concerned with the quality of their work. Hobbyists take great pride in their creations, and share them with family and friends. Professionals spend hours researching design ideas before starting to work on a project. Professionals will be meticulous about all aspects of their work, from selecting the right materials to finishing it.
Where can I find my woodworking tools?
There are many places you can get everything you need, and you don't have to go far. For example, you could visit local hardware stores or look online at websites like Amazon.com.
You can also search flea and garage sales for furniture and other materials that can be reused.
How much do hobbyists need to invest in starting a business?
You will need capital to purchase the tools and supplies you need to start your woodworking business. Start by getting a small circular saw saw, drill press or circular saw. These items aren’t too expensive so you won’t have to break the bank.
How often should new supplies be purchased?
You'll probably have to replace some of your tools over time. If you're using hand tools, you'll need to sharpen them regularly. You'll also need to replace parts if you use power tools. Try spreading your purchases over a few months so you don't buy too many at once.
Statistics
- Average lumber prices rose about 600 percent between April 2020 and May 2021. (familyhandyman.com)
- Overall employment of woodworkers is projected to grow 8 percent from 2020 to 2030, about as fast as the average for all occupations. (bls.gov)
- Most woodworkers agree that lumber moisture needs to be under 10% for building furniture. (woodandshop.com)
- The best-paid 10 percent make $76,000, while the lowest-paid 10 percent make $34,000. (zippia.com)
External Links
How To
How to join two pieces of wood together without nails
Woodworking is an enjoyable hobby. Woodworking can be a fun hobby because you can work with your hands to make useful objects from wood. However, there are times when you want to join two pieces of wood together without having to use nails. This article will show you how to do it to make your woodwork projects look great.
The first thing you'll need to do is cut off any rough edges from your pieces of wood before joining them together. Do not leave any sharp corners as they could cause problems down in the future. Once you have done that, you can begin gluing your boards together.
If you are working with hardwood, only one side should be glue. If you are using softwoods such pine or cedar, glue should only be applied to one side. Apply the glue to the boards and press them down until they are securely attached. Make sure you let the glue dry before moving on to the next step.
After you've glued your boards, you'll want to drill holes into the joints where you plan to insert screws. Depending on what type screw you choose, the size of these holes will depend on how big they are. If you plan to use a 1/2 inch wood screw, drill a hole at least 3/4 inches in depth.
Once you've drilled your holes, you'll want to drive the screws through the joint and into the backside of the board. Don't hit the board's surface. You could damage the finish. Don't drive the screws too far into the end. This will avoid splitting in the wood's ends grain.
You'll need to protect your completed project from the elements. You can either seal the entire piece of furniture or cover the top. You'll want a product that lasts for many years. You can choose from oil-based varnishes or polyurethane, shellac and lacquer as examples.
These products can be found in most home improvement shops. Be sure to choose the right one for your project. Don't forget to keep in mind that some finishes are toxic. So, always wear protective gear when handling them.