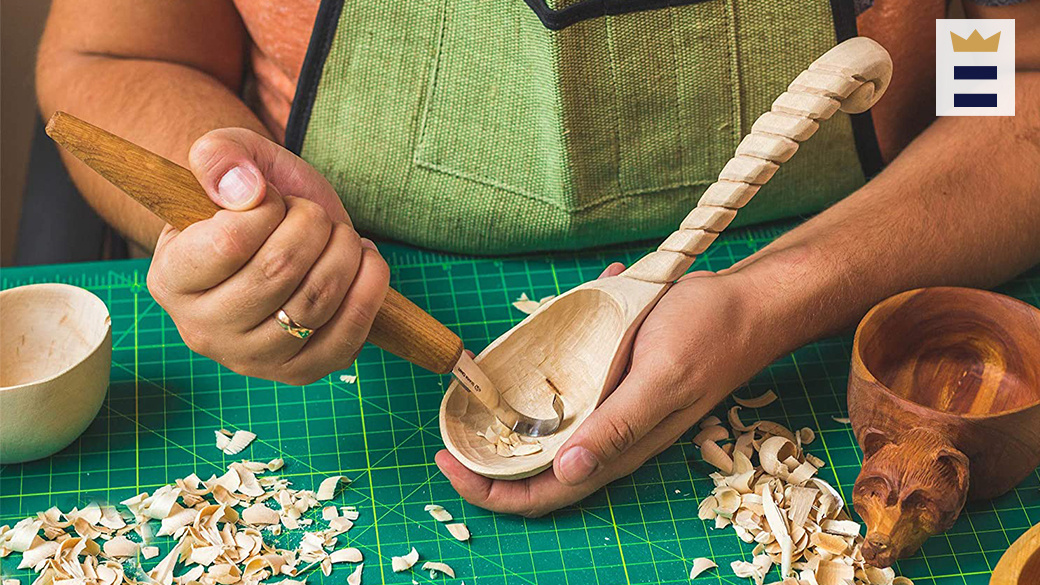
You've likely tried chip carving before and it's not an easy task. There are many different styles and techniques that you can try, but which one is best? What tools are necessary? This article will share my tricks and tips for carving chips and help you choose the right one for you. You can carve potato chips in a traditional or more modern way, but there are some essentials that will help you succeed.
Traditional
Chip carving is one of oldest forms of woodcarving. It requires a straight-edged knife but a skew-ground or offset blade knife can also be used. Chip carving is a technique that involves making small, triangular incisions into wood in order to create a pattern. This art form originated over 1,000 years ago. It was so popular that many designs looked the same across nations, making it difficult to tell which one was which.
As wood carving spread across the globe, generations passed down the skills. Chip carving was a popular way to decorate furniture in Sweden. Eventually, schools were opened to teach the craft. Modern chip carvers have benefitted from the skills and knowledge of centuries-old carvers. Over the years, knowledge and experience was passed from apprentice to student. It's a lifelong process that continues today.
Form free
This DVD will teach you how to chip carve. Murray Taylor has created a DVD that shows you how create both freeform and geometric carvings. It is an excellent introductory project with plenty of information. English and NTSC versions of the DVD are available. The DVD is also available in widescreen and stereo. Artisan Media Ltd. is the owner of DVD. It is also available in MP4 format for Windows or Mac computers.
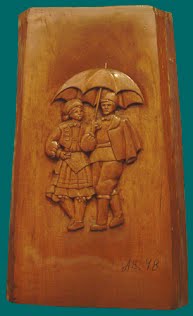
Triangles, lines, and circles are the most common shapes used in geometric chip carving. You can combine different styles with this technique, which allows you to create unlimited patterns and shapes. This type of chip carving is also known as free-form chip carving. No matter what shape your chips are, they will add beauty to any room. You can incorporate multiple techniques into one piece by free-form chip carving.
Techniques
Chip carving has been around since the beginning of time. These examples can be found all around the world. In the South Pacific Islands, for example, chip carving has been found on boat paddles and ceremonial tool handles. These carvings were probably done using bits and pieces of bone, seashells, or shark teeth. This book shows how to create stunning designs using a variety chip carving techniques.
You can easily carve chip if your follow some basic steps. The first of these is to know how to carve the fine triangle. This pattern can be understood and executed quickly. To carve this pattern you will simply need to make several triangles. Then, repeat this process. It doesn't have to be boring. Simply by changing the angles, you can create amazing patterns.
Tools
Lora Irish offers an online seminar for free that will cover the basics of chip-carving. She shows you how to use a variety of carving tools and materials, such as a chip, stab, and detail knife. Irish will also cover the various types of wood carving tools in this free seminar. The list below will help you choose the right tool to suit your carving needs. These tools can create simple shapes and designs. Or, you can work more intricately to create more intricate designs.
Special geometry is required for chip carving knives. It measures about one and a half inches in length with a narrow, curving back edge. This allows for precise incisions. It is also important to choose a sharp, needle-sharp point so that the edges meet perfectly. Chip carving knives are also made of stainless steel and come with a sharp tip. A chip carving knife should have a sharp tip that can cut through a piece of wood.
Getting started
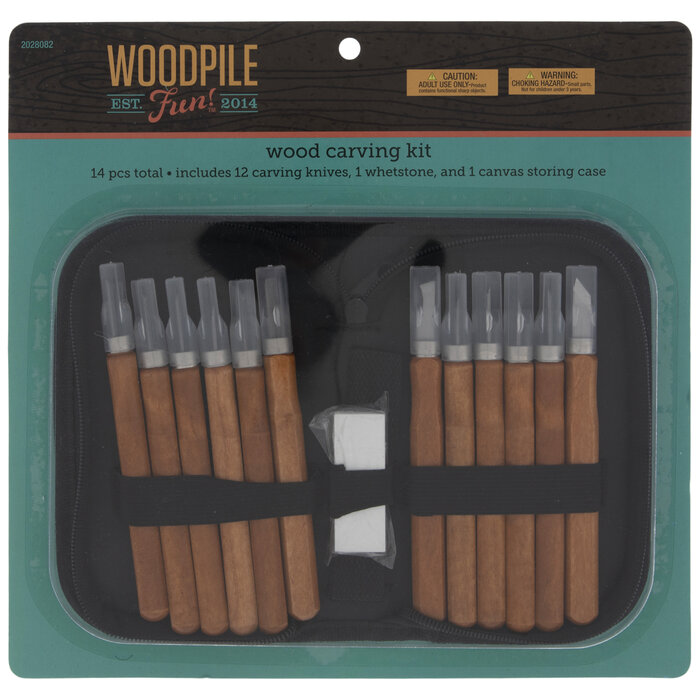
When getting started with chip carving, you must first learn about its methodology. This process varies based on the type of carving that you intend to do. However, these principles will help you ensure your work is accurate. Chip carving is the art of cutting fine patterns in wood. Here are some steps to help you create your first chip-carving.
It is important to properly sharpen a chip carving knife. Chip carving knives will have bevels along their blades, which indicates they are primary chip carving knives. The sharpening rock is shaped as a diamond, and can produce effective edges. Place the stone at a 10 degree angle. The stone will sharpen the chip carving knife and chip carving tool at the same time.
FAQ
How much should a woodworker charge per hour?
The hourly rate of a professional woodworker depends on many factors including experience, skill level, availability, location, etc.
The average hourly rate for a skilled woodworker ranges from $20-$50 an hour.
A less skilled woodworker can charge as low at $10 an hour.
Do you know anything more about woodworking?
It is easy to underestimate the amount work involved with furniture construction. Finding the right wood is the hardest part. There are so many wood options that it can be difficult to choose the right one.
Another issue is that wood does not have the same properties. Some woods will crack or warp with time. Others will split or crack. These are important considerations to make before you purchase wood.
Does it take a genius to make woodworking work?
No. Woodworking does not require any special skills. Anyone can learn to use basic powertools and techniques to create beautiful work of art.
What is the difference between a hobbyist woodworker and a professional woodworker.
Hobbyists enjoy creating things out of wood. Professionals tend to focus on the quality. Hobbyists are proud of their creations and will often share them with family members and friends. Professionals will spend hours researching designs before they begin working on a project. They'll pay great attention to details, from choosing the most suitable materials to finishing the work perfectly.
How can you calculate the woodworking price?
It is essential to calculate costs as accurately as possible when pricing any project. Always ensure you are getting the best possible price for materials. You should also consider other factors that could impact the cost of your project, such as experience, skill level, time, and money. Our guide to the average household DIY task price will give you an idea of how much it costs to complete different types of woodwork projects.
How can I keep my shop organized?
A designated place to store your tools is the first step towards keeping your workshop clean. Make sure your tools are clean and free of debris and dust so they can be used properly. Pegboard hooks can be used to hang tools and accessories.
Statistics
- Overall employment of woodworkers is projected to grow 8 percent from 2020 to 2030, about as fast as the average for all occupations. (bls.gov)
- Average lumber prices rose about 600 percent between April 2020 and May 2021. (familyhandyman.com)
- Most woodworkers agree that lumber moisture needs to be under 10% for building furniture. (woodandshop.com)
- The best-paid 10 percent make $76,000, while the lowest-paid 10 percent make $34,000. (zippia.com)
External Links
How To
How to make wood joint
This tutorial will help you join two pieces of wooden together. We'll use the "pocket hole joint," which means we drill holes in the wood and then glue them together. If your wood has a straight grain, smooth surface, you can use this method. You may want to consider other methods, such as dowel joining. These are the steps
-
Drill Pocket Hole Joints. To start, measure and mark where you want to put the pocket hole joint. Then drill 3/4 inch deep holes into the ends of each piece of wood using a jig saw or handheld drilling machine.
-
Sand Smooth. You can sand the edges of the wood to ensure that it doesn't split.
-
Glue both sides together. Apply glue to both the ends of the wood. Let it sit for about 5 minutes before clamping the pieces together.
-
Clamp the Pieces Together. After the glue has dried you can attach the pieces to form a flush joint.
-
Trim Joinery. After the glue dries, trim any excess wood around your joint.
Make sure to leave enough room between the pieces so that you can turn them inside and out.