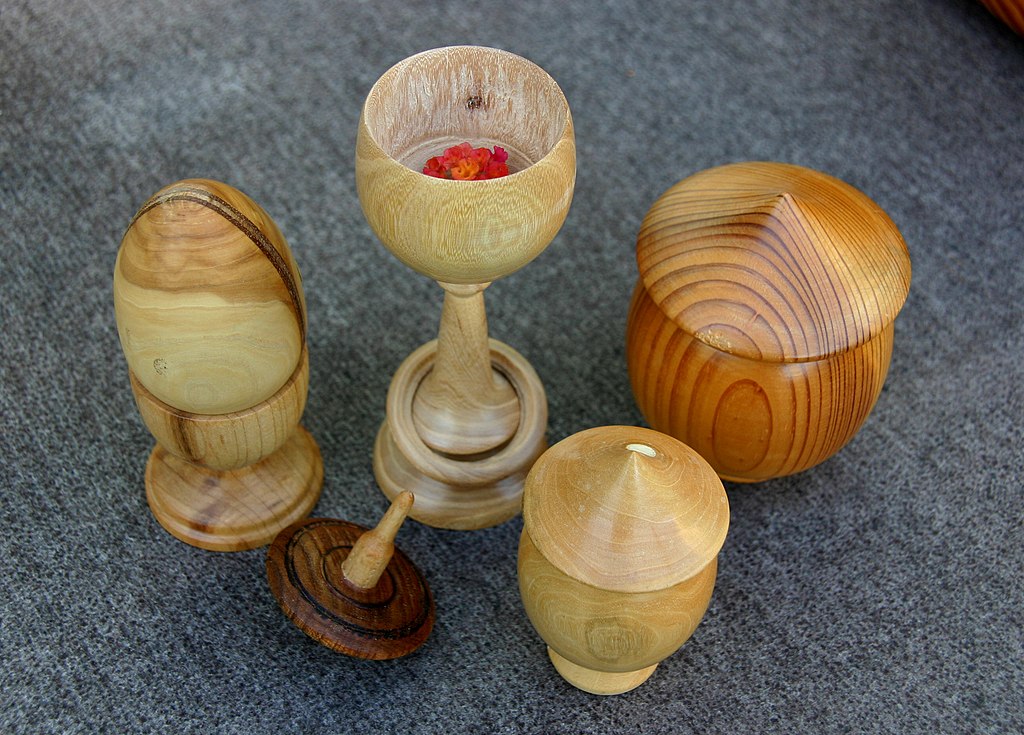
Before moving on to more difficult projects, beginners should be familiar with the basics of wood turning. Start by turning a simple project like a handle to hold a hammer. Beginning woodworkers can take on a variety smaller projects to help them get comfortable with the craft. After mastering the basics, more advanced woodworkers can move on to more difficult projects. Listed below are some of the basic techniques and tools used in woodturning.
Spindle turning
Creating a spindle starts with a square blank. Mount the blank between the headstock and tailstock using a roughing gouge. Measure the blank to the desired size using a ruler. Next, use a parting instrument to adjust the spindle to achieve the desired diameter. Use a caliper to measure the diameter of each individual section, then move the tool rest in between each groove until the desired diameter is reached.
Woodturning is a rewarding hobby. But it's important to be safe while turning. Many techniques work well for spindle production, safe turning, and you can apply the knowledge to many different projects. This article will not cover all aspects of woodturning safety but it will be a great starting point for your project. You should always consult a professional for more information regarding safety.
Working with softwood
Wood can be divided into two categories: hardwood and softwood. Hardwoods can be turned and include oak, maple, and hickory. Softwoods, on the other hand, are suitable for carving. European yew is great for making bows or musical instruments. While softwood is ideal for crafting furniture, it is not recommended. Engineered timbers such as yellow pin are not good for turning.
Softwoods can retain their pitch pockets which can lead to problems in your finished work. Even after air drying, this wood can still leak pitch. Therefore, you should protect your clothes and other surfaces against the wood pitch. Pre-stain conditioner can be applied to softwood before any stain can be applied. Pre-stain conditioning will penetrate the wood's open fibers and act as a barrier.
Lathe speed limit
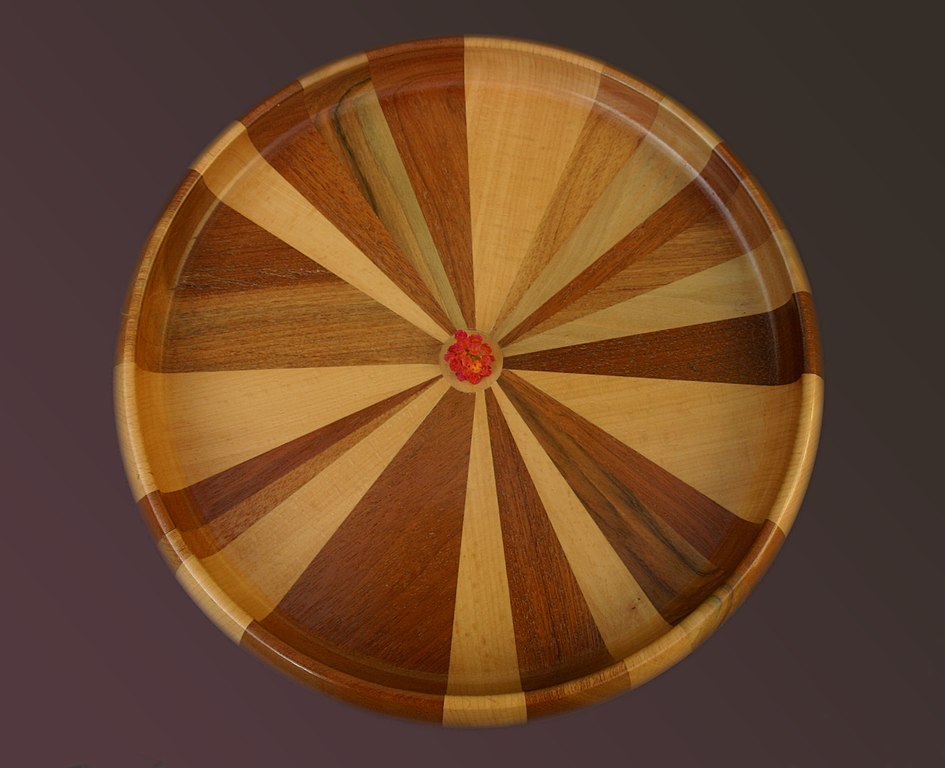
Wood turners are unanimous in agreeing that the maximum lathe speed to achieve a certain diameter should be between 6 000 and 9000 rpm. There are many variables to be aware of, including the particulars of the workpiece. If the piece is 3 inches in diameter, the speed should be 2,000 RPM. However, a 10 inch work piece would run closer to 600 RPM. Limiting factors for lathe speed include the vibration that the workpiece can withstand. Therefore, a lower RPM would be best.
The right speed for your lathe should enable you to turn blanks with minimal vibration. If the workpiece is small or requires careful shaping, a lower speed setting might be better. The work will be smoother if you use a higher speed setting. Try different speeds to find the right speed for your woodturning projects. A smoother result will be obtained if you turn at higher speeds.
Tools to Use
This list contains some of the most important tools for woodturning projects. A skew (or a tool equipped with a beveled cutter edge) is used for shaping wood. This tool is great for cutting long ribbons out of wood. Additionally, a skewchisel works better to make a flat surface for turning bowls.
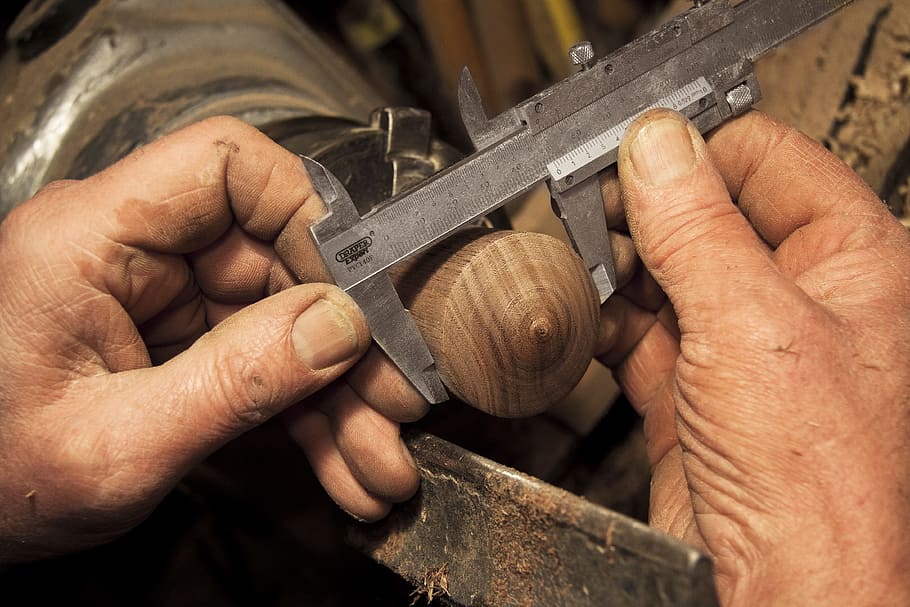
For woodturning, it is crucial to invest in quality tools. Buying cheap tools is not a good idea, as they don't hold an edge as well. High-speed steels require a sharpening device. You should also purchase a grinder, which has a decent 8" diameter, to make your work easier to sharpen.
FAQ
Do I need to be a genius to succeed in woodworking?
No. Woodworking does not require any special skills. Anyone can learn to use basic powertools and techniques to create beautiful work of art.
Is it difficult to start my woodworking business?
It can be difficult to start your woodworking business. There are many regulations and legal requirements that you will need to comply with. However, it doesn't necessarily mean you must go through all the hassle of setting up a business. Many people join already-established businesses. This will allow you to avoid paying membership fees and taxes.
Do you have the skills to learn woodworking?
You can learn everything best by doing. Woodworking requires patience, practice and skill. It takes time to master any craft.
To actually learn something is the best way. Start small and then build upon what you've learned.
Statistics
- Woodworkers on the lower end of that spectrum, the bottom 10% to be exact, make roughly $24,000 a year, while the top 10% makes $108,000. (zippia.com)
- The U.S. Bureau of Labor Statistics (BLS) estimates that the number of jobs for woodworkers will decline by 4% between 2019 and 2029. (indeed.com)
- Most woodworkers agree that lumber moisture needs to be under 10% for building furniture. (woodandshop.com)
- In 2014, there were just over 237,000 jobs for all woodworkers, with other wood product manufacturing employing 23 percent; wood kitchen cabinets and countertop manufacturing employing 21 percent. (theartcareerproject.com)
External Links
How To
How to make wood joints
This tutorial will show you how to join two pieces of wood together. The "pocket hole joint" is a method whereby we drill holes into the wood and glue them together. This method works great if your wood is straight and smooth. If your wood isn't straight or flat, you might want to try another method, such as dowel joinery. Here are the steps
-
Drill Pocket Hole Joints. Start by measuring and marking the spot where the pocket hole joint will be placed. You will then drill 3/4" deep holes through each piece of wood with a jigsaw, handheld drilling machine, or hand-held drill.
-
Sand Smooth. Sanding the wood's edges will ensure that the joint doesn't split.
-
Glue Together Apply glue to both ends of the wood. Allow it to sit for approximately 5 minutes before you clamp the pieces together.
-
Clamp the Pieces Together. After the glue has dried completely, you can clamp the pieces together until they are flush.
-
Trim Joinery. After the glue dries completely, trim off any excess wood around the joint.
To be able to turn the pieces inside-out, leave enough room between them.