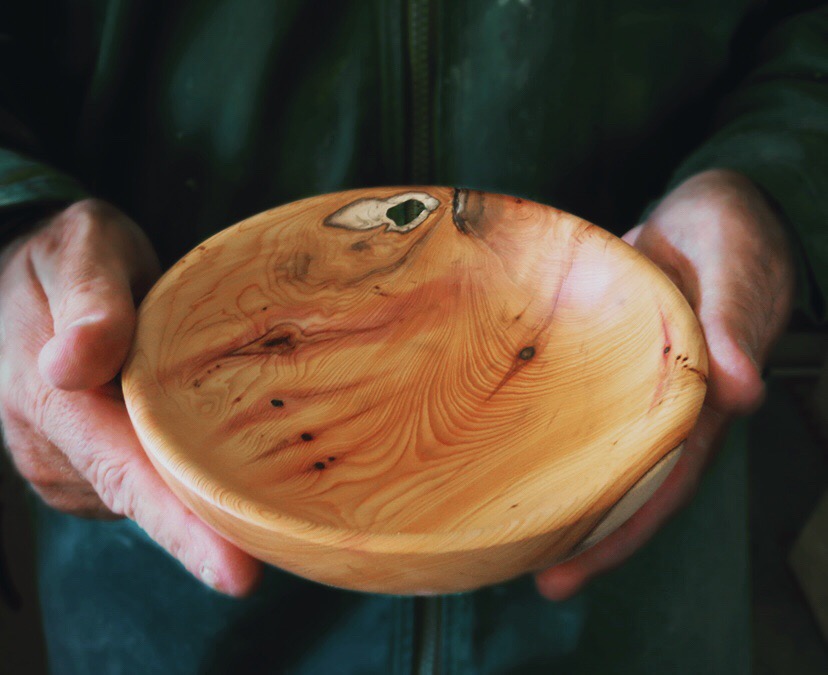
In order to support the mission of Eagle Ranch, the Chattahoochee Woodturners worked with the organization to build a woodturning studio on the school campus. Woodturners received an Educational Opportunity Grant from American Association of Woodturners as well other donations for the construction of the facility. Local woodturners donated equipment as well as tools to help get this project off the ground. Students can visit the woodturning workshop, which is open to everyone.
Hark woodturner
Around eight years ago, Hark approached Hark after taking a class and started the woodturning course at Harvard University's Mather Building. Hark said yes to the offer and agreed to teach the class at Harvard. After several unsuccessful attempts to teach the course in Harvard, Hark eventually found an old lathe from a basement of a neighboring house. That spring, his first Harvard class started. Students from all Harvard Houses are invited to the woodturning workshop's classes today. He also continues teaching woodturning on weekends.
In addition to teaching classes, Arthur and Pamela have traveled to woodworking symposiums and trade shows in search of new audiences for their work. They have met a wide variety of world-renowned artists and have hosted them as their guests. The studio has hosted a variety of woodturning workshops featuring a wide range of artists and styles. It also sent a Knight Commander and Commander to the Norwegian Woodturning Cruise every three years.
Tools
Safety gear is an essential item to have in your woodturning workshop. To protect your eyes and prevent the glares of sand from damaging your skin, you may need safety goggles or a helmet. Sharpening tools can also be an investment. You will also need safety gear. A jigsaw and lathe are essential to sharpen lathe blades.
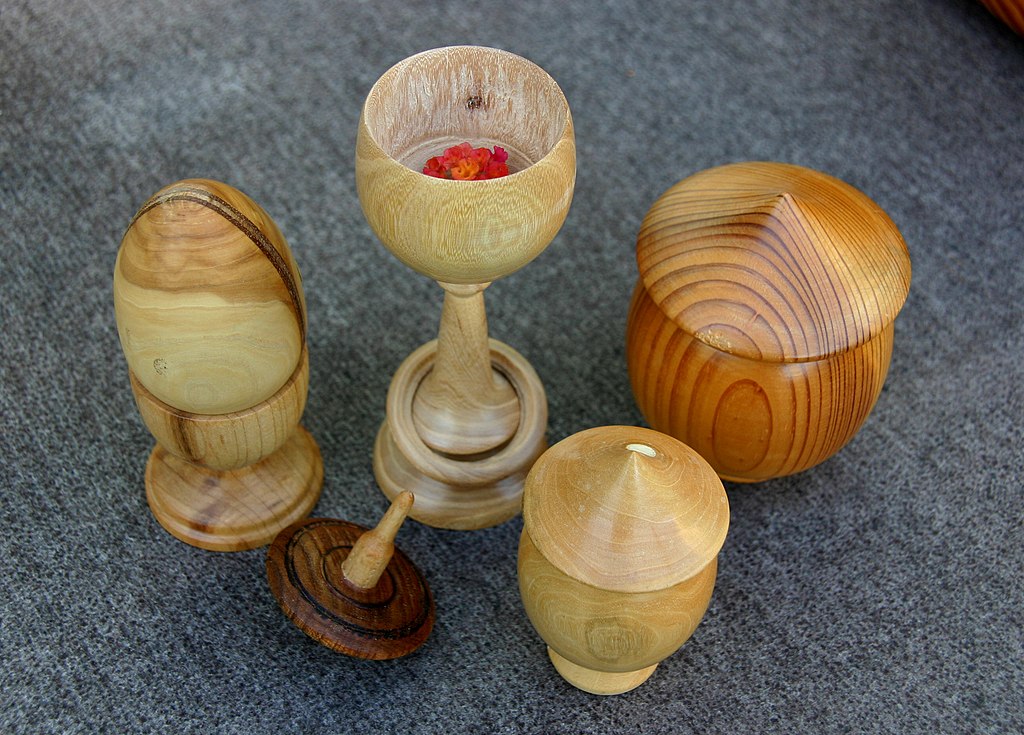
A drill, a wrench, and a banjo are three of the most important tools you will ever need. The banjo lets you slide your tool along the lathe bed supporting the toolrest. This allows you the best possible position for your turning tool. Modern lathes come with a locking mechanism that locks the banjo. These tools will help you create your custom creations.
Techniques
Whether you are interested in pursuing hobby woodturning or have an established professional practice, it is important to know the proper tools and techniques for woodturning. These tools are crucial for creating functional and beautiful pieces that will be both functional and attractive. These tools are available online and at your local woodworking store. It is not an easy process to turn wood, but it is worth the time.
A woodturning class can be a great way for beginners to get started. A workshop will cover everything you need to know, including safety gear and choosing the right tools. A lathe will be used by participants. The course will teach you how to properly use tools and allow you to try out different techniques. Your projects will vary depending on your skills, and can include carving mallets or making bottle stoppers or bowls.
Class size
If you are new to woodturning and are interested in learning the basics, a beginner's workshop at a woodturning studio in Durham, NC, may be perfect for you. You will learn basic techniques and tools. The class will also include several projects. Safety will be the focus of this class. Make sure you bring a helmet and protective gear.
Small classes allow you to be more focused on each student's individual learning. You will get individual attention and plenty of time from your instructors to answer any questions. Often, there will be no more than six students in a class, so you can expect to learn at a comfortable pace. Most of the classes are project-based. Classes will typically last for two days. Private lessons can be arranged for students who are more experienced and want to focus on particular techniques.
Cost
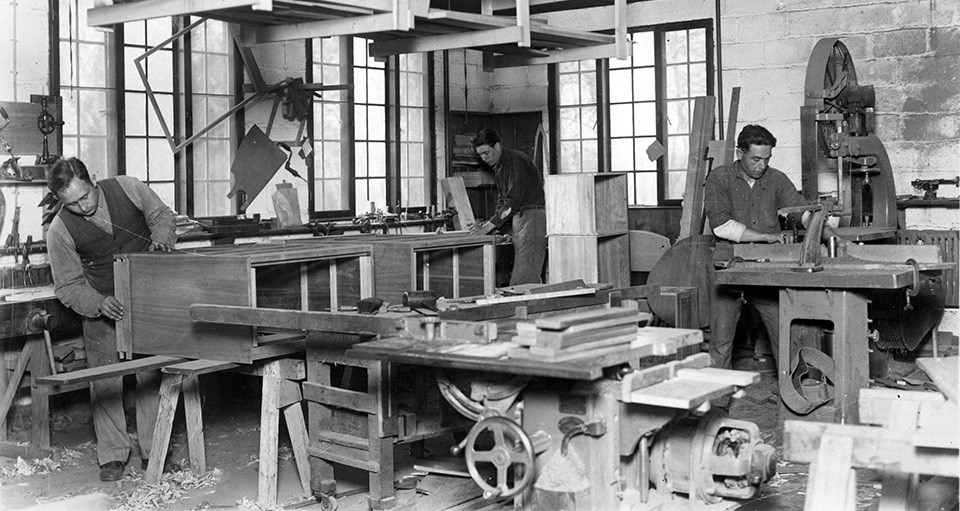
It can be costly to start your own woodturning business. Equipment and supplies can easily cost several thousand dollars. The best way to save money on these expenses is by selling your products at a reasonable price. In fact, selling your finished products will double or even triple your profits. While high-end pieces are a great way to promote your art and generate profits, you may also want to sell items at a lower price point. Simple items are still possible to sell, even though expensive items take longer to manufacture. In fact, they can sell out within the first day of a two-day art show.
A class will help you get started in woodturning. This will include safe use of tools as well as proper sharpening. Then you can move on to more challenging projects and learn advanced tools and techniques. A typical cost for an introductory class in woodturning is $75 for Mather residents and Harvard associates. All materials and tools included in the cost. In addition, you'll also receive a list of nearby hotels.
FAQ
How long does it take to finish a piece of furniture?
It depends on which wood you choose, how complicated your design is and what amount of finishing you apply. For example, hardwoods require more maintenance than softwoods. Hardwoods are also more expensive than softwoods. But they last longer, and resist moisture better. The average time it takes to finish furniture is one week to three weeks.
Do you have the skills to learn woodworking?
Learning by doing is the best way of learning anything. Woodworking is an intricate art form that requires practice, skill, patience, and experience. It takes time to master any craft.
To actually learn something is the best way. Start small and then build upon what you've learned.
Which material would you recommend for woodworking lessons?
Start with softwoods, such as pine or poplar. When you feel confident with these two, move on towards hardwood.
Where can I find my woodworking tools?
You can find everything you need in many places. You can visit your local hardware stores, or you can look online at sites like Amazon.com.
You can also search flea and garage sales for furniture and other materials that can be reused.
What is the difference in a hobbyist and professional woodworker?
Hobbyists are passionate about making things from wood, while professionals tend to be more focused on the quality and craftsmanship of their work. Hobbyists usually take pride in their creations and often share them with friends and family. Professionals will spend hours researching designs before they begin working on a project. They will pay attention to every detail, from selecting the best materials to finishing the project perfectly.
How can a novice woodworker make it big?
Many people learn how to make furniture in order to set up an online business. There are other ways to make money if you're just starting out building furniture than selling on Etsy. You could sell at craft fairs or local events. For those who want to build their own furniture, you might offer workshops. If you have experience as a carpenter or builder, you might consider offering services such as remodeling homes or creating custom pieces for clients.
Where do I start with woodworking?
The best way to learn how to build furniture is by building furniture. While you will need tools, mistakes are inevitable, but you will learn the ropes if you persevere.
Begin by choosing the project that you want to finish. You can make a simple box or a large entertainment center. Once you have settled on a specific project, it is time to find a woodworker in your area who is experienced in such work. Ask them for their advice about the tools and where they can be found. Maybe you can ask the person if they know of anyone who does this sort of work.
Statistics
- The U.S. Bureau of Labor Statistics (BLS) estimates that the number of jobs for woodworkers will decline by 4% between 2019 and 2029. (indeed.com)
- Average lumber prices rose about 600 percent between April 2020 and May 2021. (familyhandyman.com)
- Most woodworkers agree that lumber moisture needs to be under 10% for building furniture. (woodandshop.com)
- The best-paid 10 percent make $76,000, while the lowest-paid 10 percent make $34,000. (zippia.com)
External Links
How To
How to drive a nail through wood
It is essential to pick the right size and style of hammer before you can drive a nail in wood. Claw hammers include mallets, claw hammers (sledgehammers), mallets, ball-peen hammers, hatchets, and mallets. Each kind of hammer has its own advantages and disadvantages. A clawhammer works best when hitting something hard like nails. However, it can sometimes be difficult to see exactly where the strike is going. A sledgehammer is great for hitting large areas at once, but it's too heavy to use effectively for smaller tasks.
Place your hand flat on the side of your chosen hammer so that the handle rests in your palm. Hold the handle in your hand, but don’t force it too hard that you break. The hammer should be held straight up with your wrist relaxed. Swing the hammer back towards the ground, with your aim at the middle of the nail. The impact of the hammer hitting the nail should be felt. Try practicing with a block to help you master the art of swinging a stick.
The hammer should be held close to your body when you are ready to begin driving the nail. Position the nail, so it's perpendicular to the surface of the wood. Your eyes should be focused on the nail's tip. Swing the hammer forward, and then move the hammerhead. You can repeat this several times, increasing your swing speed. Once you've mastered the technique, try adding power to your swings. To make it more powerful, hold the hammer up high to your shoulder and then bring it down. This will help you put more energy behind each of your moves.
Once you've nailed the first hole, remove the hammer from the nail. To pull out the remaining nails, use a screwdriver or pry bar. To avoid splitting the wood, make sure the nail heads are not touching the board's surface.