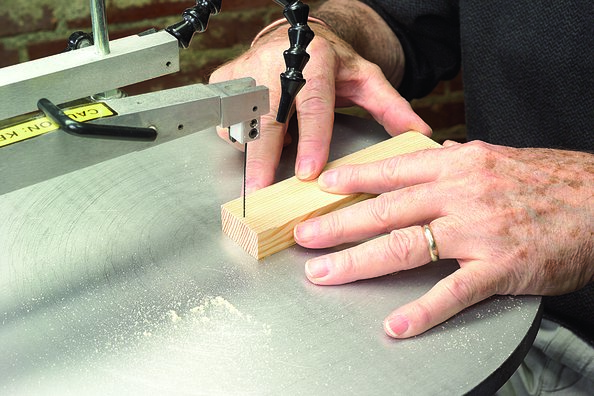
Making scroll saw train designs requires consideration of many factors, such as what wood to use, how many sheets to cut and how big the pattern should be. Scroll saw pattern books make it easier to complete the project. The patterns can also be printed on the opposite side of the page, so that they can be cut directly from the book. These books are great for both experienced and novice scroll saw users.
Wood requirements
Scroll saw train patterns require a variety of wood types. Woods such as cherry, walnut, and oak are some of the most sought-after options. Birch is another excellent choice, but it tends to absorb stain in irregular patterns. You may also need exotic woods such as mahogany and walnut for other projects. Avoid using fir or luan plywood. Cherry and walnut both have low prices and high strength-to-weight.
Beginning woodworkers shouldn't attempt intricate patterns before they become more proficient. Beginners should keep to the lines drawn onto the wooden surface and then work their way back. Scroll saw blades are not able to cut straight lines. To avoid causing damage to the blade, use your hand to guide the saw onto the table. It is a good idea to know the maximum wood your scroll saw can cut.
Pattern size
Scroll Saw Train Patterns can be found on a number of websites. There are two options depending on the type of project you're working on: a large-scale yard art image, or a small scrollsaw shelf project. Scroll saw train patterns come in various sizes to fit any project. For your convenience, the patterns can be divided onto multiple A4 and letter-sized sheets. These designs can be printed out and cut right from the book.
A simple project is the best way to get started with scroll saws for beginners. There are many popular scroll saw patterns, including a coaster and hanger sets, a VW Beetle plaque, a VW Beetle plaque, a heart jewelry tree, and even a VW Beetle placket. These patterns can be printed for free. Once you've found the perfect pattern, start building! There are so many possibilities! Scroll saw patterns can be made in many sizes and shapes.
No. of sheets of paper needed
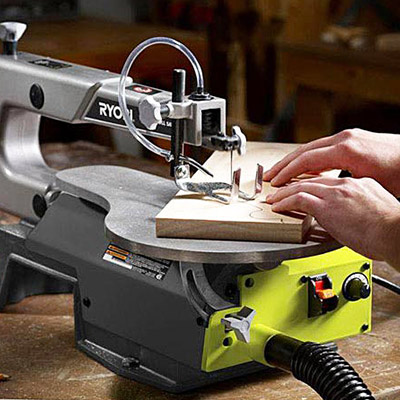
You can print out scroll saw pattern patterns to practice with large pieces. The designs are fully-sized and there are no inside cuts. These patterns are also easy to enlarge and save paper. Print one side of the pattern and cut out any pieces you require. Use the copy for practice pieces on larger projects. Keep in mind that the practice pieces you create don't necessarily have to be connected.
Clear packaging tape is an alternative. This will prevent wood fibres from sticking to your pattern. Some scroll sawers use weaker paper than regular paper, but painters masking tape is used by some. Others use a mix of clear packaging and painters' tape. In all cases, ensure you read and comprehend the instructions before using them. You will not ruin your patterns this way.
Evolution of scroll saw
Although the first patent issued for a reciprocating-steel blade in Great Britain was in 1829 the origins are unknown. The exact date of the first scroll saw's appearance in Western Europe is unclear. However, it can be dated back to prehistoric civilizations. In those times, woodworkers used knives to make intricate cuts. This method of cutting wood was called fretwork, and traces its history back to the earliest civilizations.
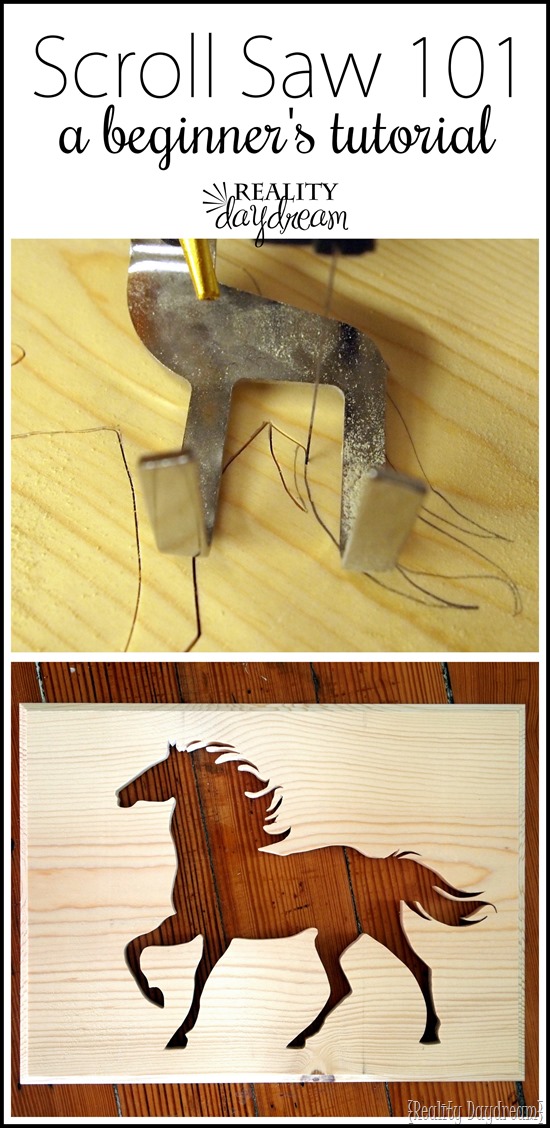
Modern scroll saws are capable of making intricate cuts because of their design features. Many scroll saws have tilting tables that allow users to make beveled edges and cut material at angles. Some scroll saws tilt up to 45°, while others tilt to the right. Others tilt to one side or the other. If this isn't enough, you can flip the material over to cut the bevel on either side. Modern models include an integrated sawstand that allows users to work more comfortably while standing.
FAQ
Where can I find free woodworking plan?
Free woodworking plans are available online. You don't even need to buy books or magazines. Just search Google. Search Google for "free woodworking" to see hundreds of sites that provide free plans.
How can a novice woodworker make it big?
Many people want to open an online furniture business and are learning how to build it. If you are just starting to build furniture, there are many other ways to make money than selling on Etsy. You could sell at craft fairs or local events. You could also offer workshops to help others learn how to make their own furniture. Consider offering your services if you have previous experience as a builder or carpenter.
What kinds of woods are good for making furniture?
Woods are classified according their hardness. Softwoods can be pine, fir or cedar. They're often used for outdoor furniture because they don't rot easily. You can find hardwoods like oak, maple, mahogany, teak, and others. Because they can't weather outside, they're usually used indoors.
What amount of money do I need to get started with my business?
Because each project is unique there are no exact numbers. Here are some factors to help you estimate how much money you will need.
-
Materials cost
-
Tools and equipment
-
Time spent on the Project
-
The hourly rate
-
What is your expectation for profit?
-
You can hire help, regardless of whether you have a plan.
It's a good idea for beginners to start with small projects like frames and boxes. As you gain more experience, you will be able tackle more complicated projects.
Where can I find my woodworking tools?
There are plenty of places where you can find everything you need to start out. For example, you could visit local hardware stores or look online at websites like Amazon.com.
You can also look for used furniture at flea markets or garage sales.
Statistics
- Woodworkers on the lower end of that spectrum, the bottom 10% to be exact, make roughly $24,000 a year, while the top 10% makes $108,000. (zippia.com)
- Overall employment of woodworkers is projected to grow 8 percent from 2020 to 2030, about as fast as the average for all occupations. (bls.gov)
- The best-paid 10 percent make $76,000, while the lowest-paid 10 percent make $34,000. (zippia.com)
- If your lumber isn't as dry as you would like when you purchase it (over 22% in Glen Huey's opinion…probably over 10-15% in my opinion), then it's a good idea to let it acclimate to your workshop for a couple of weeks. (woodandshop.com)
External Links
How To
Tips on how to drive a nail in wood
First, choose the right size and type of tool to drive a nail through wood. Claw hammers include mallets, claw hammers (sledgehammers), mallets, ball-peen hammers, hatchets, and mallets. Each type of tool has its advantages and drawbacks. For example, a claw hammer works best when you want to hit something hard, like nails; however, it's difficult to control precisely where the blow lands. A sledgehammer is great for hitting large areas at once, but it's too heavy to use effectively for smaller tasks.
After selecting the right hammer, you will need to place your hand flat against one side of the head. The handle should rest comfortably in your hands. You can grip the handle with your fingers, but not so tight that it causes injury. Keep your wrist relaxed and the hammer straight up. Then swing the hammer back toward the ground, aiming for the center of the nail. You should feel the impact from the hammer striking a nail. Try practicing with a block to help you master the art of swinging a stick.
The hammer should be held close to your body when you are ready to begin driving the nail. To ensure that the nail is perpendicular on the surface of the wooden floor, position it. Keep your eyes focused directly on the tip of the nail. Swing the hammer forward, then follow through with the motion of the hammerhead. Continue this motion several times, slowly increasing the speed of each swing. When you are confident with the technique, add power to your swings. Try holding the hammer above your shoulder and bring it down forcefully. This way, you'll be able to put more energy behind your blows.
Once you've made the first nail hole, take out the hammer. To remove the remainder of the nails, you can use a screwdriver/pry bar. To avoid splitting the wood, make sure the nail heads are not touching the board's surface.